Vibration Monitoring in Critical Equipment with Swift Sensors
Vibration monitoring in critical equipment is essential for ensuring operational safety and efficiency in industries that rely on large, complex machinery. Abnormal vibrations are an early indicator of mechanical issues, and detecting them can prevent costly damage, unplanned downtime, and even workplace accidents. Swift Sensors provides wireless vibration monitoring solutions that allow companies to continuously monitor critical equipment, detect anomalies, and intervene proactively to ensure optimal equipment performance.
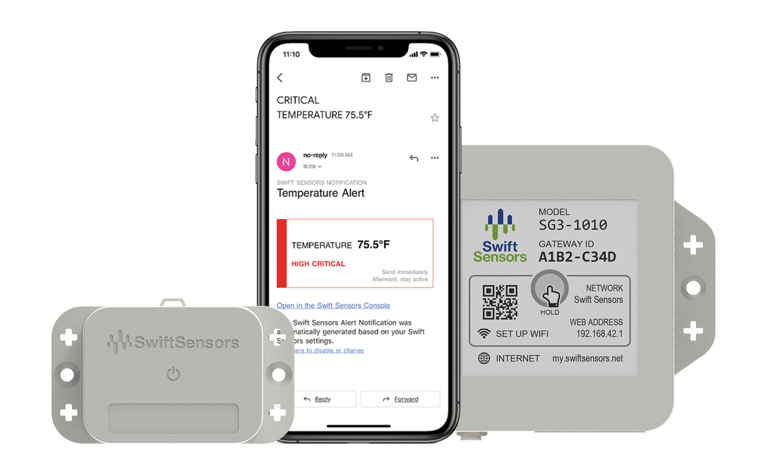
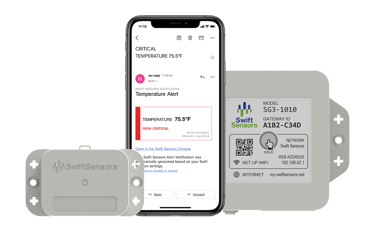
Specific Applications for Vibration Monitoring with Swift Sensors
1. Production Machinery in Heavy Industry
Vibration monitoring in production machinery used in heavy industries (e.g., motors, generators, pumps, and compressors) is essential for preventing failures that could halt production lines and cause significant financial losses.
Early Fault Detection: Vibration sensors detect abnormal oscillations at an early stage, signaling wear on mechanical components. This allows maintenance teams to intervene before a fault becomes critical.
Reducing Downtime: Identifying and addressing mechanical issues in advance prevents unplanned shutdowns, reducing productivity losses and ensuring continuous operations.
2. Mobile and Construction Equipment
In construction and the mobile equipment sector, such as excavators, cranes, and heavy-duty trucks, vibrations can damage critical components and affect equipment stability.
Vibration Monitoring in Harsh Conditions: Construction equipment is often exposed to extreme working conditions. Swift Sensors’ wireless sensors can monitor vibrations in these environments and provide real-time data, enabling rapid intervention and preventing premature equipment wear.
Operational Safety and Efficiency: By detecting abnormal vibrations early, sensors contribute to operational safety, protecting both the equipment and the personnel operating it.
3. Energy Industry and Power Generation Equipment
In power plants and industrial production facilities, equipment like generators and turbines are constantly subjected to intense mechanical stress. Vibration monitoring is vital for preventing breakdowns that could lead to costly shutdowns.
Preventing Catastrophic Failures: Sensors detect any abnormal increase in vibration, which may indicate a serious mechanical problem. This allows maintenance personnel to take immediate action to avoid severe damage.
Maximizing Equipment Lifespan: By continuously monitoring vibrations, companies can implement predictive maintenance, reducing wear and extending the lifespan of critical equipment.
4. HVAC and Ventilation Systems in Commercial and Industrial Buildings
Large HVAC (heating, ventilation, and air conditioning) systems in buildings require careful vibration control to operate efficiently and to ensure occupant comfort.
Lower Maintenance Costs: Vibration monitoring allows for early detection of imbalances or faults in ventilation and air conditioning systems, optimizing maintenance interventions and reducing maintenance costs.
Energy Efficiency: Well-maintained HVAC equipment operates at maximum efficiency. Vibration monitoring contributes to lower energy consumption and improved system performance.
Key Features of Vibration Monitoring with Swift Sensors
Wireless Monitoring and Cable-Free Installation:
Swift Sensors are fully wireless, which allows for quick installation on various industrial equipment without the need for cables or complex infrastructure. This feature makes them ideal for installations with hard-to-access or mobile equipment.
With no cables required, the sensors can be mounted directly onto equipment, offering flexible placement and enabling rapid adjustments based on monitoring needs.
WiFi Connectivity and Centralized Platform:
Vibration sensors transmit real-time data via WiFi to a centralized platform, accessible from any internet-connected device (computer, tablet, smartphone). This enables continuous monitoring of critical equipment, even remotely, providing complete visibility of equipment status.
The centralized platform allows real-time vibration data analysis as well as tracking historical trends, enabling informed maintenance decisions for equipment.
Automated Alerts for Critical Vibration Thresholds:
Swift Sensors enable the setting of critical thresholds for vibration levels. If these thresholds are exceeded, the system sends automatic alerts via SMS, email, or push notifications, alerting maintenance teams for immediate intervention. These alerts reduce response times and help prevent equipment deterioration.
Automated alerts are essential for preventing unplanned production stops and for protecting valuable equipment from excessive wear or damage.
Long Battery Life:
Powered by durable batteries, the sensors can operate continuously for extended periods, minimizing the need for frequent maintenance and allowing constant equipment monitoring without interruptions.
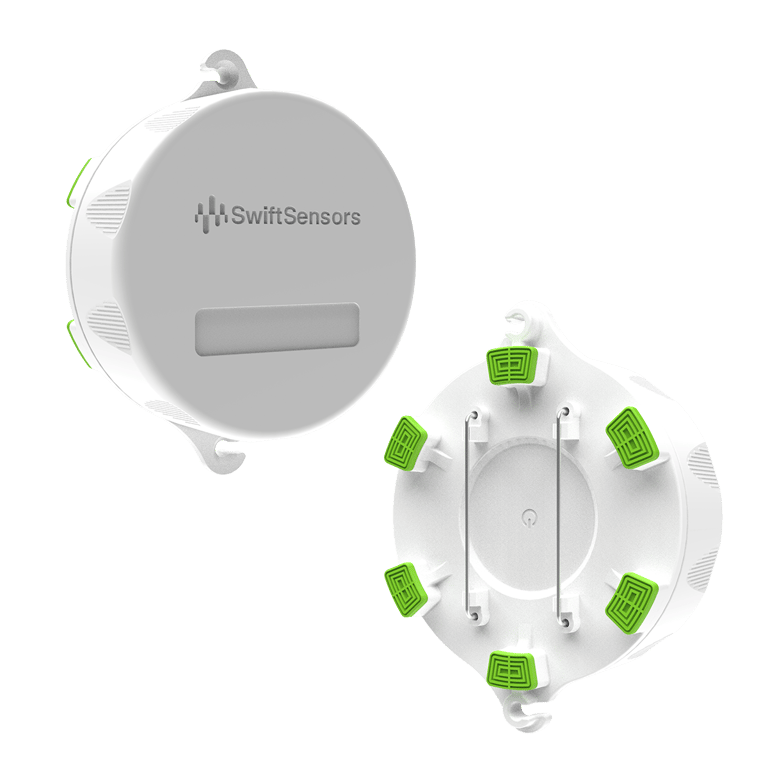
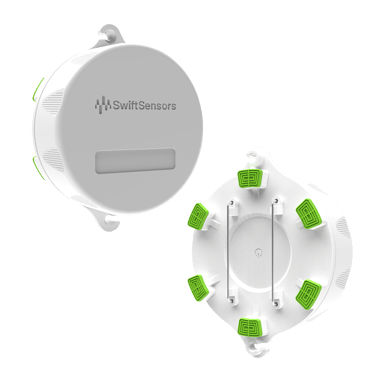
Benefits of Vibration Monitoring with Swift Sensors
Predictive Maintenance and Cost Reduction: Continuous vibration monitoring enables companies to implement a predictive maintenance program, preventing failures and reducing repair and replacement costs.
Equipment and Personnel Safety: Early detection of abnormal vibrations helps prevent major mechanical problems, protecting both equipment and operator safety.
Operational Efficiency and Downtime Reduction: Identifying problems before they cause stoppages allows for operational continuity and increased productivity.
Real-Time Data and Accessibility: With Swift Sensors, vibration data is accessible anytime and from anywhere, allowing companies to make quick, informed maintenance decisions.